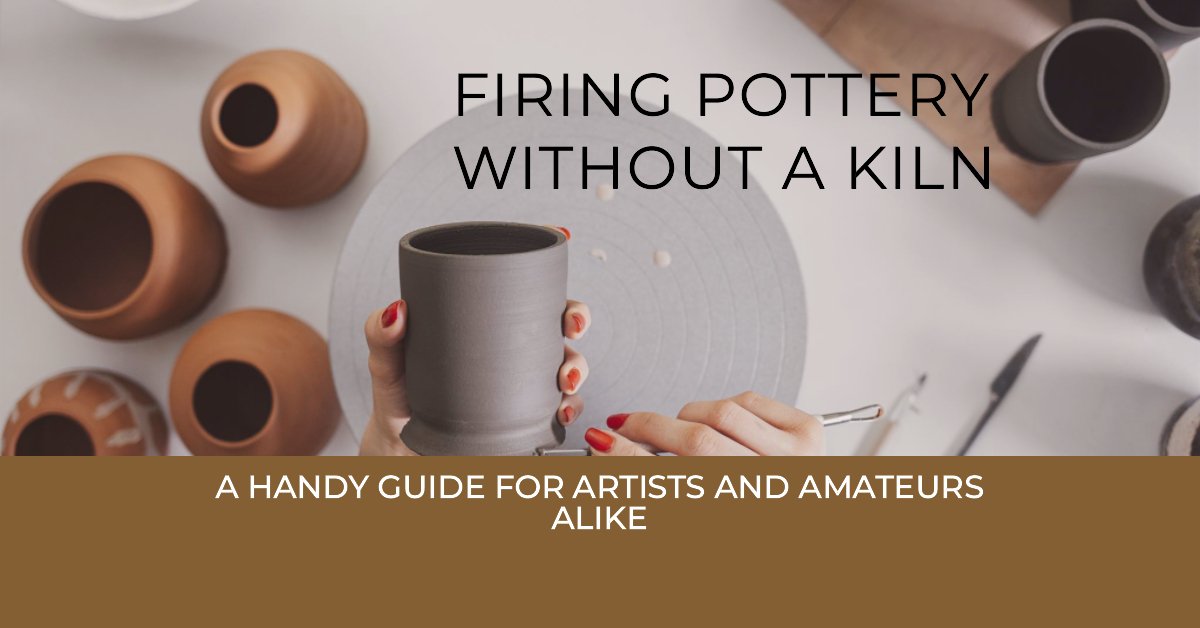
How to Fire Pottery Without a Kiln
For many budding pottery creators, the urge to craft stunning ceramic work is inevitably met with a stark reality - Pottery Kilns, the traditional method of firing clay, can be expensive and are often large and hard to accommodate. Fear not, at Kiln Crafts, we're here to provide both products and solutions for every stage and type of ceramic preparation.
However, not all pottery requires a fully equipped studio and a top-of-the-line kiln. While we have an extensive collection of Pottery Kilns for Home and several meticulously designed Pottery Kilns, we understand that sometimes, you need an alternative solution. This article seeks to guide you on how you can fire pottery without a kiln.
Alternatives to Traditional Kilns
Traditional Electric Pottery Kiln and Top Loading Pottery Kilns provide excellent heat distribution and consistency, which are crucial for successful pottery firing, but they're not the only options out there.
Pit firing is an alternative method for firing pottery, one of the oldest known to man, dating back as far as 29,000–25,000 BCE. This method does not require elaborate and heavy machinery like our esteemed Falcon products – from the compact Falcon 50l Front Load Pottery Kiln to the spacious Falcon 500l Front Load Pottery Kiln.
Instead, pit firing only requires a hole in the ground – the 'pit', your pottery, and combustible materials such as wood and leaves to create heat. Here is a short step by step guide on how you can achieve this:
- Dig a pit in your backyard deep enough to house your pottery.
"Remember, to pit fire pottery, the pots should lie flat and not touch each other. This will ensure even heat distribution."
Once you've got your pit, your pottery, and your combustibles ready, you can begin the firing process.
The Pit Firing Process
Start by layering your pit with combustibles. Then you place your pottery. Continue layering until you fill the pit. Light your pit and let it burn until all your combustibles have turned to ash.
"Pit firing is an organic method and each firing can yield different results; it's part of its unique charm."
Put out any remaining embers and remove your pottery once it has cooled down. A layer of soot might cover your work, but this can be easily washed off with water.
In lacking a Small Pottery Kiln, another method of firing pottery at home is through gas firing. This method uses a barbecue gas grill or a gas burner as the heat source. Be sure to use low fire clay for this method to ensure successful results. The Falcon 65l Front Load Pottery Kiln is a wonderful representation of using a heat source, but in this instance, you can tap into your home resources.
The adaptability of these methods allows the creator to explore the essence of pottery making in its various forms, unrestricted by the typical necessities commanded by a world-class assemblage of kilns.
And while we are strong advocates for professional kiln solutions like the Falcon 80l Front Load Pottery Kiln and the CU4 Home Pottery Kiln, we recognize that having a full-fledged kiln at home may not be a luxury everyone can afford.
In the spirit of reinvention and resourceful creativity, we encourage craftsmen to also explore local pottery workshops offering kiln services. A community alternative that not only helps usability but also fosters creativity.
Remember, there's a joy in the process itself, regardless of the complexity of your firing methods. So enjoy your ceramic journey, and let your creativity manifest.
Utilizing Local Pottery Workshops
The necessity of having a separate studio set up your home isn't a factor limiting your creativity. Local pottery workshops are a thriving community of artists, each offering a variery of services including access to professional Kiln equipment. Be it an Ecokiln or a sleek Harrier Pottery Kiln, there's nothing comparable to an in-person firing experience.
"Every pottery artist knows the anticipation of waiting for their pieces to emerge from the kiln, changed forever by the heat and flames inside."
With community accessibility, you can enjoy this sensational moment while not having to worry about housing and monitoring a Home Pottery Kiln yourself. This not only saves you money but also grants you the access to expert guidance and a chance to share your experiences with other artists. It's a win-win. In fact, it's a norm in this craft industry to offer kiln hire services. As potteries need to be fired at a high temperature which can't be achieved in domestic ovens, local workshops welcome all enthusiasts with open arms.
The Process at Workshops
Once you finish your pottery making process at home, wrap it up carefully. As fresh pottery is vulnerable to damage, handle it delicately. Reach out to your local pottery workshop or a community studio and ask about their kiln services. Depending upon the size of your pottery, and the temperature required to fire it, they will quote a price.
"Having your work professionally fired ensures the longevity and integrity of your pieces."
After the completion of the firing process, collect your pottery. Don't rush, as it can take several hours for pottery to cool down sufficiently and safely after being fired. Then, you can take your work home and display it with pride and joy. Our Falcon 250l Front Load Pottery Kiln is a perfect example of the professional touch you can anticipate at these workshops.
Conclusion
In essence, firing pottery doesn't always have to involve a Pottery Kiln. You can also make use of these innovative methods, such as pit firing or gas firing. And when you want that professional finish without owning a Top Loading Pottery Kiln, your local pottery workshops are there to provide the kiln you will need.
So dive into the magical world of pottery making. Let your creative juices flow and give form to your imagination. Be it a home-made kiln, a community kiln at a workshop, or one of our top-notch kilns, remember, it isn't about the kiln that you use but rather the piece of art that you create.
"At the end of the day, the real joy of pottery comes from the creative process and the sense of accomplishment of making something beautiful from a humble piece of clay."
And at Kiln Craft, we provide both the tools and the information to ensure you make the best out of your pottery experience.